Tips to Ensure Quality in Aluminum Jars Orders
Aluminum packaging has extraordinary advantages: recyclability, durability, and aesthetics. However, careful attention to detail is required to achieve high-quality aluminum packaging. We know that aluminum box packaging will use ink printing as a process. So, how to avoid errors in this process and provide higher-quality aluminum box packaging products? There are several points we can share:
1. Compatibility between materials and ink
One of the main factors of successful packaging design is to ensure that the ink adheres reliably to the aluminum surface. For example, using a single-component ink specifically designed for plastics may result in weaker adhesion, especially on aluminum. Aluminum surfaces require ink specifically designed for metal, such as two-component metal ink, to withstand wear and prevent issues such as fading and scratches over time.
2. Surface treatment of aluminum
Implement surface treatment processes during the production process to ensure consistent ink adhesion. The pollutants on the surface of aluminum can also reduce the adhesion of ink. Pre-treating the surface with a cleaning solution (such as alcohol) is crucial for removing dust, oil, or other residues, which can improve the adhesion of the ink. This preprocessing step is crucial in improving durability, especially on curved surfaces where achieving uniform ink application is more challenging.

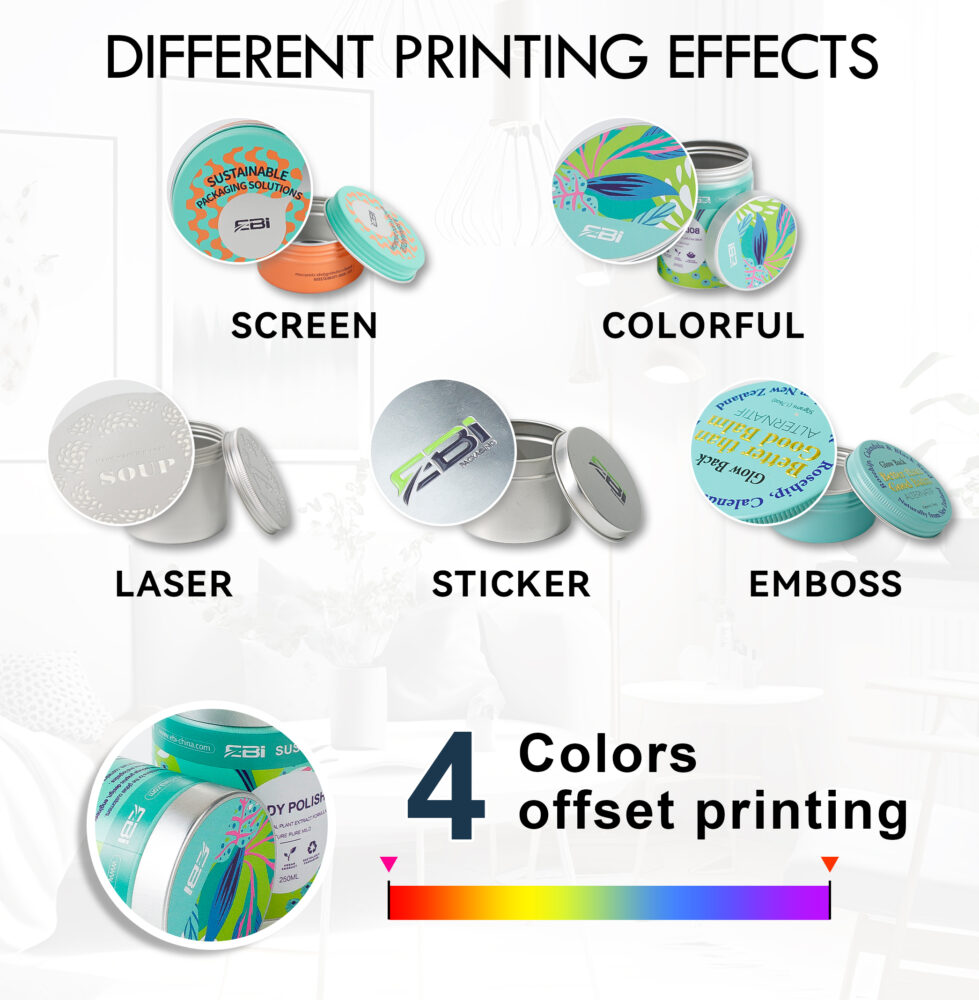
3. Optimize the curing process
Standardize the curing process through precise temperature and time settings to ensure consistency in ink quality on aluminum packaging. Proper temperature control and baking time are crucial for forming a long-lasting bond. Based on our experience, the optimal curing temperature for aluminum screen printing is 140 ° C and the curing time is 20 minutes. This process helps to enhance the adhesion between ink and aluminum, even on curved surfaces.
4. Conduct a comprehensive quality inspection
Comprehensive quality control should be established at every stage of production to detect potential issues early. This includes line testing, third-party inspection as well as pressurization testing for printed packaging examples. As shown in a recent case, even with preliminary inspections, additional testing can still identify issues that may arise after shipment.
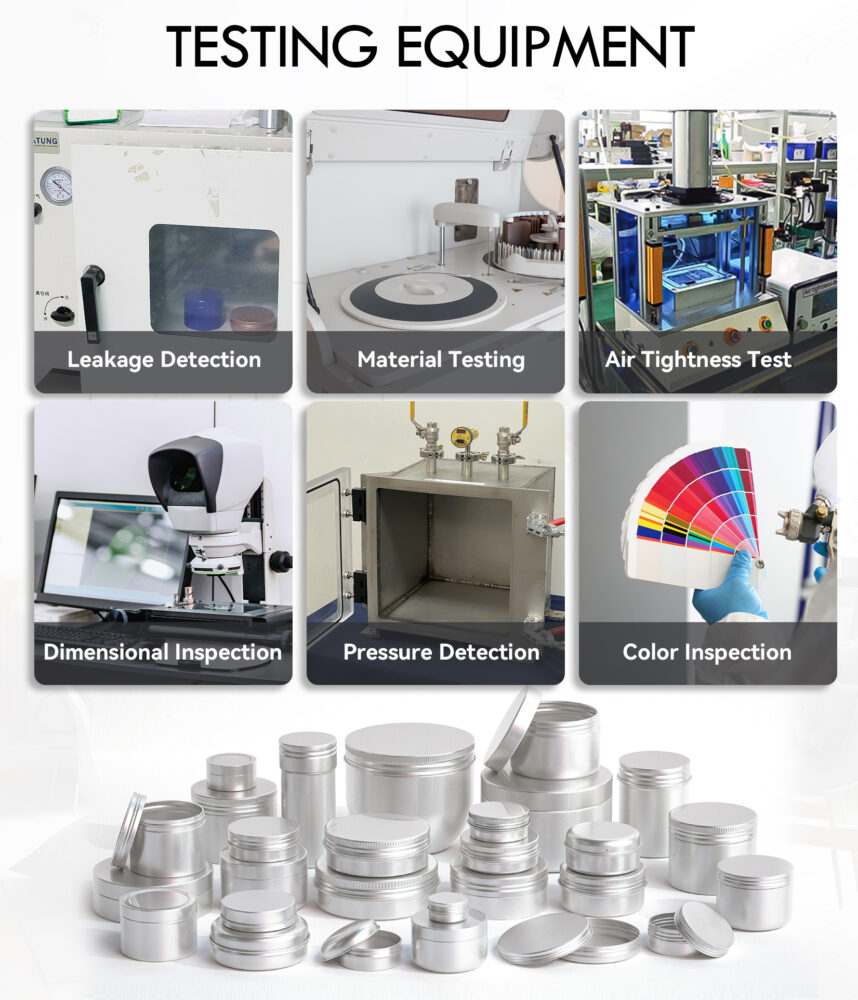
5. Transparency in customer communication
When problems do arise, transparency is the key to maintaining customer trust. Provide timely solutions and actively communicate with customers. Let customers know the measures we have taken to improve this issue. This helps maintain confidence and strengthen partnerships. Proactively identifying and solving problems is essential for the company to achieve long-term sustainable development, and improve product quality and image.
Conclusion:
High-quality aluminum packaging requires professional knowledge, precision, and proactive quality management. Focusing on ink compatibility, surface treatment, curing process quality control and delivery ensures businesses avoid common pitfalls while meeting customers’ expectations. Adopting these measures not only ensures successful orders but can also create stronger long-term relationships between the business and its customers.